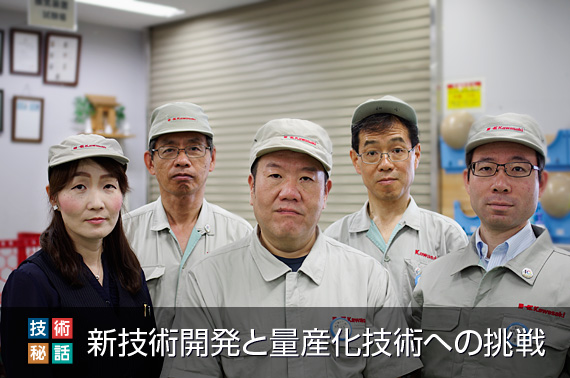
2007年度より川崎重工業(株)向けに納入を継続している『川崎MAGターボ
®』の主要装置は、当社からの販売累積台数がまもなく200セットを迎えます(
2008年7月のShowroom VOL.22で販売開始を紹介)。当社では『川崎MAGターボ
®』の中の主要なシステムである磁気軸受制御装置と電力変換装置の量産を担当しています。
その『川崎MAGターボ
®』の事業の開始当時は、システムの量産化体制を整備することから始まり、その後、軌道に乗せるまで数々の試練があったそうです。今回は、開発・製品化に携わった関係者の方をお招きし、当社の担当者と共に開発時の秘話や、当時の苦労話をお聞きしました。
今回お話をお聞きした方々:
川崎重工業(株) エネルギー・環境プラントカンパニー
エネルギーシステム総括部 空力機械部 ブロワ設計課 課長 山内 正史氏
川崎重工業(株) 技術開発本部 システム技術開発センター
インテグレーションシステム開発部 部長 阿部 一広氏
川重テクノロジー(株) システム開発事業部 機電システム部 第一課 中川英彦、澤田正志
川重テクノロジー(株) システム開発事業部 機電システム部 製造課 小倉一樹、内藤敦子
Q. 川崎MAGターボ®とはどのような装置でしょうか
下水処理場の微生物の棲む“生物反応槽”に空気を吹き込む装置
山内課長:『川崎MAGターボ
®』は下水処理場で使われる装置です。例えとしてよいかどうかわかりませんが、熱帯魚を飼育する際のエアーポンプの巨大なもの、と考えると、イメージしやすいでしょうか。下水処理場の一連の設備の一つに生物反応槽がありますが、ここに活性汚泥という泥水をためています。これに下水を導き “空気を吹き込んで”下水と活性汚泥を混ぜ合わせます。活性汚泥は微生物が棲んでいる泥水で、下水中の汚れの主成分である有機物などを微生物が食物として分解し、取り込んで沈殿するので水がきれいになります。“生物反応槽”の微生物を活性化するために空気を吹き込む装置が、曝気用ブロワ『川崎MAGターボ
®』になります。
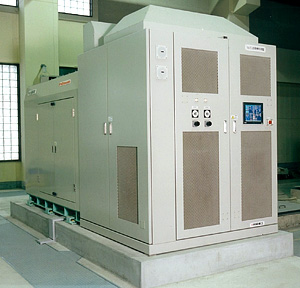
川崎MAGターボ
Q. 社内では川崎MAGターボを、“マグ”って呼んでいますが、『川崎MAGターボ®』の名前の由来は
MAGnetic bearing + ターボブロワ
山内課長::『川崎MAGターボ®』では羽根車付の電動機を数万rpm(rpm:1分間あたりの回転数)で高速回転させます。そのため、電動機ロータを“磁気軸受”により、機械的に非接触に、所定位置に数μm精度で浮上させています。磁気軸受(MAGnetic bearing)の“磁石“と回転式送風機(ターボブロワ)を合わせて、MAGターボという名称になりました。名称を決める際にはカンパニー内でいくつかの候補があり、開発関係者の投票で決まったと記憶しています。
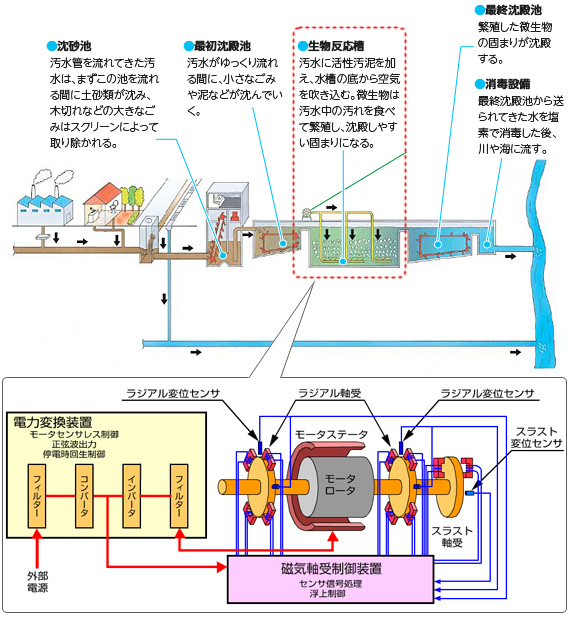
川崎MAGターボ システム構成
Q. 他に何か特長はありますか
自社開発の高性能インバータと制御装置
山内課長:
①省エネルギー
下水処理場は都道府県の公共施設の中でもエネルギー消費が多く、例えば東京都では全消費電力量の約1%を占めています。下水処理場の設備の省エネルギー化で電力料金が、年間数千万円の費用削減になるとの試算もあります。下水処理場の中で最もエネルギー消費量の多い曝気用ブロワ設備では、省エネルギー化が必須となります。『川崎MAGターボ
®』では、磁気軸受で機械的な摩擦を無くすと共に、モータの動力を供給する電力変換装置部分に高性能インバータ(自社開発)を採用することにより、エネルギー損失を徹底的に抑制しています。
②安全性
また、停電時は電動機を発電機として制御装置の電源として利用します。これにより、突然の停電でも、電動機ロータの浮上状態を維持することができ、無停電電源装置(UPS)などの付帯設備がなくとも、安全に運用いただけます。
③省メンテナンス
羽根車をロータ軸端に直接取り付けることで増速歯車やカップリング、潤滑油装置などの付帯設備無しで運用できるため、省スペースを実現することができます。加えて、機械的な摩擦が無いため、長期間メンテナンスを行う必要もありません。
当社は、磁気軸受制御装置、電力変換装置を納入させていただいております。ここからは、2001年度から2016年度まで当社に在籍され、川崎MAGターボ®開発に携わられた阿部部長にお話をうかがいます。
Q. 当社が川崎MAGターボを開発するきっかけは
機械ビジネスセンターと技術開発本部との共同開発
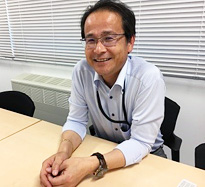 阿部部長 |
阿部部長:2004年頃だったと思います。当時の機械ビジネスセンターブロワ設計部門より、特殊なモータと軸受の技術調査を依頼されました。調査結果に対して相当厳しく査定され、調査内容をどんどん深めた結果、最終的には1冊の本のようになりました。その後、2006年頃から、『川崎MAGターボ
®』の開発を行う事となり、機械ビジネスセンター、技術開発本部と共に、川重テクノも共同開発者として参加させて頂く事にしました。川重テクノからは私の他数名でスタートしました。
Q. 開発当時から関わっていたメンバーが現在当社に所属するメンバーですね。
担当した開発業務
中川主幹:電力変換装置の量産化に携わりました。量産化に合わせて、試験用に実験棟が新設されたこともあり、出荷試験設備の計画や構築も行いました。
澤田主幹:当時、私はシステム技術開発センターに在籍し、電力変換装置、磁気軸受制御装置の開発に携わりました。
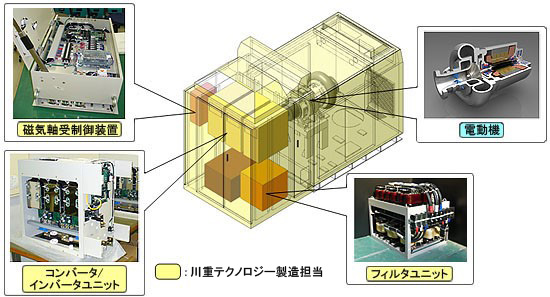
当社製造範囲 右下は、メンテナンスツール(制御システム部制作)
Q. 当時の苦労話を教えていただけますか。
量産化への挑戦 ~体制・品質管理・コストダウン~
阿部部長:
①体制の構築
開発段階でも色々とありましたが、私が本当に苦労したのは、“量産品の生産管理や品質管理“です。当時、川重テクノは量産品を継続的に製造・メンテナンスする体制が整備されておらず、今後の量産に向けてどう体制を整えるかをずっと考えていましたね。2008年には「私、技術職、辞めます。」と宣言して、量産化に向けてメンバーを集め、どんな管理が必要か、どんなツールが必要かを考え、少しずつ整備し、現在の「製造課」の前身組織を立ち上げていきました。
②生産管理のための仕組みづくり
品証部門も巻き込んで、図面、型式などの情報を管理するデータベース(PARKS)を開発、生産管理のための仕組み作りも行いました。また、量産当初は製品品質が安定せず、川崎重工業のカンパニーの品証部門の方からも、品質管理についてご指導いただき、モノづくりを勉強させていただきました。
③コストダウン
コストダウンにも注力しました。業者選定での部品の調達価格を下げるために、多くの協力会社と話をし、「その費用では無理です。」と何度聞いたことか。材料費の削減とは別に試験設備の構築で、試験工数の削減にも取り組みました。コストダウンを狙って、改良開発も行いましたが、納入後に不具合が発生し、結果、リコール費用が発生したこともありました。振り返れば、製品開発から生産・メンテナンスの全プロセスを肌身で学ばせてくれた貴重な案件で、今の私の基礎を作ってくれました。
製造現場の整備
中川主幹:
①一からの設計
初号機(2式)の製作と量産試験設備の構築が同時並行で進む中、MAGターボ本体の装置の形状などが確定していないころから設計を開始したため、初号機が納入されるまでに何度も修正を繰り返しました。
②人材の育成
量産設備の試験は、製造課のメンバーが単独で実施できるように教育を行いましたが、パワーエレクトロニクス機器の取扱い経験のない作業者でしたので、検査方法やパワエレ機器の取り扱い方法を伝授する際には苦労しました。なかなか試験時間が短縮できず、つきっきりで指導した結果、今では何も言わなくても出来るようになっています。
③周囲への配慮
量産当初は、電力変換装置にモータと同容量の模擬負荷を接続して量産出荷試験を、ほぼ毎日、終日運転していました。
試験中は装置からも発熱するので、夏場はエアコンもフル稼働となり、模擬負荷とエアコンで電力を存分に消費していたため、実験棟の電力メータが猛スピードで回転していたのを覚えています。(今は試験設備や試験方法を改善して省電力化したので、ゆっくり回ってます。)
また、実験棟が工場の端にあるため、電力変換装置の試験時の騒音で工場の近隣住民から苦情が来ないようソリューション事業部に協力を依頼して、騒音計測を実施しました。
問題の無いレベルたったのですが、念のため、今も夜間の試験は行わず、昼間しか試験を行わないようにしています。
納入後は、客先の環境(硫化水素などの影響)でメータリレーなどの使用している機器に不具合が発生したり、
量産開始直後に廃品種になってしまった機器もあり、部品選定の難しさを実感しています(いま現在も...)。
電子制御・ハード・ソフト技術の結集
澤田主幹:それまでシステム技術開発センター、川重テクノロジーで培ってきた電子制御・ハード・ソフトの技術を結集させる必要に迫られました。中でも数百kWで数万rpmという高速回転に対応させることと、電子制御をうまく使って僅かな隙間で浮上させることがポイントだったと思います。
Q. コスト、品質を維持しながら量産製作が継続しています。どんな取り組みを行っていますか。
生産計画のための密な情報収集
内藤係員:川崎MAGターボ
®の生産管理に携わっていますが、部品の納期管理には苦労しています。
製品納期を見計らって、協力会社からタイミングよく部品が入ってくるように調整していますが、部品納期は安定せず、また、海外製の部品は、納期の長いものが多く、思ったようにはいきません。年間の生産計画をいち早く把握するために、カンパニーを訪問して、情報入手はまめに行っています。
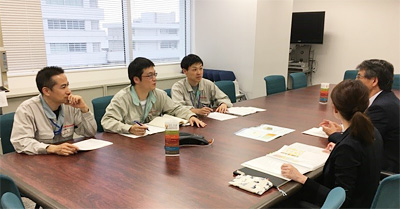
カンパニーの方との生産情報の共有(左端が山内課長)
的確なトレーサビリティ情報の提供と最適なメンテナンス方法の提案
小倉課長:納入から10年を経過しており、最近ではメンテナンス(オーバーホール)対応も始まってきています。
開発時に品証部門と協力して構築したデータベース(PARKS)に出荷時の情報が保存されています。生産中止になった部品や、改良のために変更した部品などもあり、これらの情報をカンパニーのご担当者と共有し、お客様に、的確なトレーサビリティ情報と、最適なメンテナンス方法を提案しています。
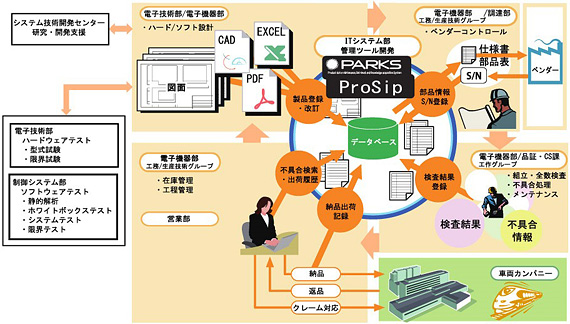
部品情報管理システム
(PARKS:Product data mAintenance, Retrieval and Knowledge acquisition System)
PARKSは当社製品
ミストリーナー(オイルミスト除去装置)の生産管理にも活用されています。
Q. 今後の展開は
海外市場の開拓と制御装置の更なる高性能化
澤田主幹:昨年度より海外輸出用の磁気軸受制御装置の開発を行っています。
先年には新しい電力変換装置を開発し、徐々に市場にも投入しています。『川崎MAGターボ
®』は現状にとどまることなく、さらに進化していきます。
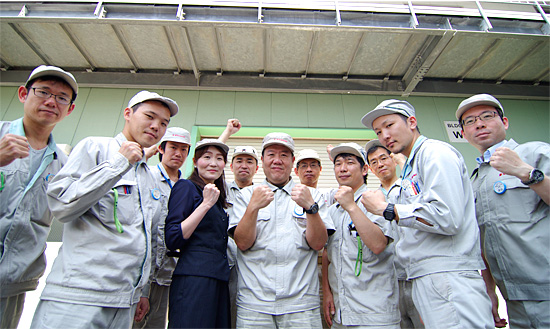
私たちはこれからも高品質・安定供給を徹底的に追求してまいります。
当社はMAGターボの電力変換装置や磁気軸受制御装置などのパワエレ応用製品、
制御システム製品や電子回路基板類の開発設計、製造を長年続けて参りました。
今後もこれまで培った量産製作のノウハウを活かし、
高品質・安定供給可能な製品を川重グループの皆さまに供給してまいります。
今後も電子・電気ハードウェアに関する製品開発でお声掛けいただければ幸いです。
聞き手:川重テクノジー(株) システム開発事業部 機電システム部 中澤 文善
商標「川崎MAGターボ®」は川崎重工業株式会社の登録商標です。
(2018/8)
問合せ先: システム開発事業部 機電システム部 第一課
中澤 文善 |
 |